In screen printing, the choice of mesh count holds a pivotal role in determining the quality and precision of the final print. This article delves into the significance of screen printing mesh counts, exploring their impact on image resolution, ink deposition, and overall print quality. Understanding these intricacies empower screen printers to make informed decisions, ensuring that each project achieves the desired level of detail and clarity.
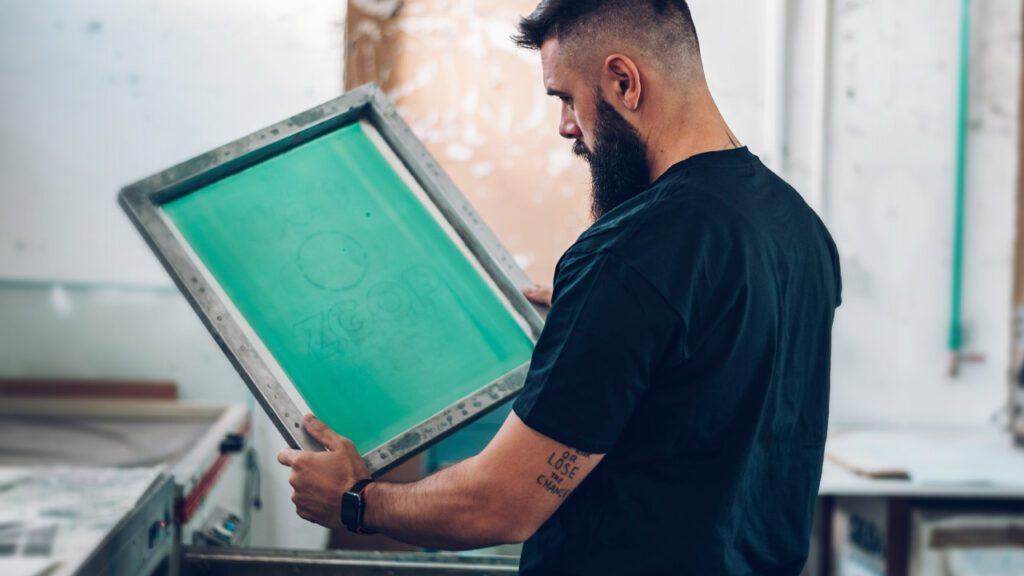
What Is A Screen Printing Mesh Count?
Screen printing mesh counts refer to the number of threads per inch in the mesh fabric used for the screen. A higher mesh count indicates a greater number of threads, resulting in a finer and tighter weave. Conversely, a lower mesh count has larger openings, allowing for more ink deposition.
The Impact Of Mesh Counts On Image Quality
Selecting the appropriate mesh count is critical for achieving optimal image resolution. Higher mesh counts, such as 230 or above, are ideal for intricate designs and fine details. They allow for a controlled and precise ink deposit, capturing nuances in the artwork with exceptional clarity. Lower mesh counts, like 110 or 156, are better suited for bold and larger designs, ensuring a higher volume of ink is transferred to the substrate.
The Impact Of Mesh Counts On Ink Deposition
Mesh counts significantly impact ink deposition, influencing the opacity and vibrancy of prints. Lower levels allow for a thicker layer of ink to be deposited, resulting in more saturated and opaque prints. Higher levels, on the other hand, facilitate a thinner ink deposit, ideal for achieving a softer hand feel and vibrant colors on lighter garments.
The Impact Of Mesh Counts On Ink Adhesion
Understanding the relationship between mesh counts and ink adhesion is crucial for screen printers. Lower mesh counts, due to their larger openings, are typically associated with better ink adhesion, especially on thicker substrates. This is because the increased volume of ink provides a stronger bond to the surface. High mesh counts, while offering finer detail, can sometimes struggle with adhesion on certain materials due to the thinner layer of ink applied. Therefore, choosing the right mesh count based on the substrate and ink type is vital to ensure optimal adhesion and durability of the print.
The Impact Of Mesh Counts On Ink Viscosity
Mesh count also plays a significant role in determining the viscosity of ink used in screen printing. High mesh counts often require inks with lower viscosity to pass through the fine mesh easily, maintaining the sharpness and clarity of the print. In contrast, lower mesh counts are compatible with thicker, more viscous inks, which are ideal for creating vibrant, bold prints with a tactile feel. Understanding this interplay between mesh count and ink viscosity is essential for achieving the desired texture and look of the final print.

Conclusion
In the world of screen printing, mesh counts are the silent architects of determining the final look and quality of the print. A nuanced understanding of how they impact the printing process empowers screen printers to make informed decisions, resulting in prints that not only meet but exceed expectations. As the industry continues to evolve, the mastery of mesh counts remains a cornerstone in the pursuit of excellence in the art of screen printing.
- Screen Printing: The Advantages Of Newman Roller Frames
- Screen Printing: Navigating The Spectrum Of Frame Sizes
- Quality vs Cost: Make Your Next Embroidery Machine A Wise Investment
- Top 5 Embroidery Machine Factors To Consider When Buying Equipment
- DTF Printing: How To Choose The Right Printer & Dryer
- DTF Printing: A Beginners Guide To Production Setup
- T-Shirt Dye Sublimation Printing With Rob Super
- 15 Must-Have Screen Printing Website Features
- The Staying Power Of Athleisure In The Apparel Decoration Industry
- How To Capture The School Market For Your Screen Printing Business